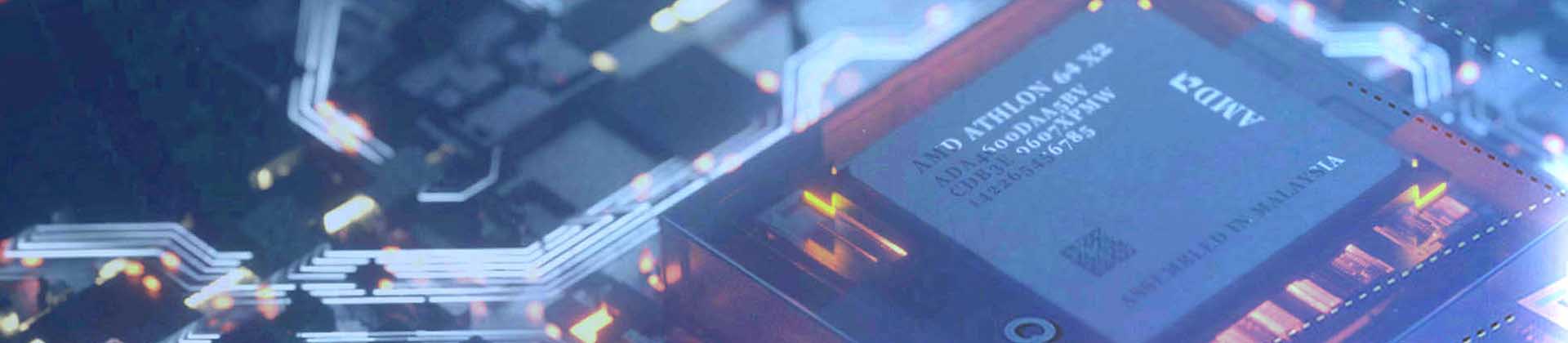
DPP-HF2P-II waterproof two-stage deviation switch NKPK1-12-30
DPP-HF2P-II waterproof two-level deviation switch two-level deviation switchUsed for conventional belt conveyors: underground, cableway support belt conveyors: ship loading and unloading system; Stacking/reclaiming conveyor; Tilt and shuttle conveyors; Crane, excavator, boom limit: skirt feeder/conveyor: heavy-duty limit switch detects the deviation of the tape, which is a protective device for automatic alarm and shutdown of the tape machine control
- DPP-HF2P-II waterproof two-stage deviation switch
- ZHUOXIN
- 24-380v
- IP65
- TT, Paypal, Credit card, Western union
- +86-15163766288
- DPP-HF2P-II waterproof two-level deviation switch two-level deviation switchUsed for conventional belt conveyors: underground, cableway support belt conveyors: ship loading and unloading system; Stacking/reclaiming conveyor; Tilt and shuttle conveyors; Crane, excavator, boom limit: skirt feeder/conveyor: heavy-duty limit switch detects the deviation of the tape, which is a protective device for automatic alarm and shutdown of the tape machine control
Description
DPP-HF2P-II waterproof two-stage deviation switch DPP-HF2P-II waterproof two-stage deviation switch DPP-HF2P/II is a type of sensor used as a protective device for belt conveyors. It is specifically designed to detect when the running tape deviates, the edge of the tape drives the vertical stick to rotate and squeeze to tilt. If the tilt angle of the vertical stick is greater than the first level action angle, the switch sends a set of switch signals; If the vertical stick continues to tilt more than the second level action angle, another set of switch signals will be output. Two sets of switch signals can be used for warning or shutdown respectively to protect the belt conveyor and personal safety. Basic principle: When the conveyor belt deviates during operation, the conveyor belt touches the switch roller and causes the roller to deflect. When the roller deflection angle reaches level 1 switch angle, the switch sends an alarm signal. When the conveyor belt deviates seriously and reaches the second level switch angle, the switch sends a stop signal to automatically stop the conveyor belt due to deviation fault. When the deviation fault is eliminated and the tape machine is running normally, the switch vertical roller can automatically reset and return to the initial state. Installation and adjustment: 1. The deviation switch should be set on both sides of the conveyor belt, and the vertical rollers should be perpendicular to the edge plane of the conveyor belt, with both sides of the conveyor belt located at 1/3 of the height of the vertical rollers. The distance between the vertical roller of the deviation switch and the normal position of the conveyor belt should be 50-100mm. The number of deviation switches should be determined based on the length, type, and layout of the conveyor. Generally, it should be set at the head, tail, convex arc section, concave arc section, and in the middle position of the conveyor. (Note: When the conveyor is long, one pair can be installed every 30-35 meters in the middle position of the conveyor.) 4. The deviation switch should be connected to the middle frame of the conveyor through an installation bracket. The switch bracket should be welded to the conveyor frame after the conveyor is installed. The deviation switch and the deviation switch bracket are fixed with bolts. The eccentric sensor DPP-HF2P/II, also known as the eccentric rotor collision sensor, is used to monitor the device of the rotor spindle. The dynamic measurement of the belt conveyor can also be used for continuous monitoring of general small machinery. This provides important information for early identification of various mechanical faults· Synchronous vibration of shaft, oil film instability, rotor friction, component loosening, bearing sleeve loosening, compressor kicking vibration, rolling component bearing failure, radial preloading, internal/external misalignment, bearing Babbitt alloy wear, excessive bearing clearance, radial/axial balance (air blocking) plug wear/failure, coupling locking
Tags
Get the latest price? We'll respond as soon as possible(within 12 hours)