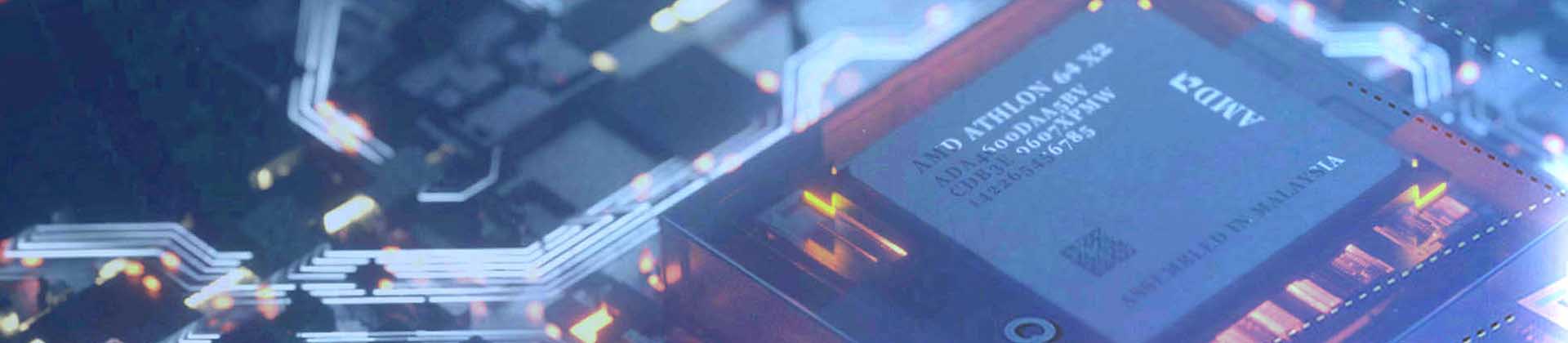
Proximity sensor XS2 30BLNAL2C C24V
The proximity sensor XS2 30BLNAL2C C24V consists of three main parts: oscillator, switch circuit, and amplifier output circuit. The oscillator generates an alternating magnetic field. When the metal target approaches this magnetic field and reaches the sensing distance, eddy currents are generated within the metal target, leading to oscillation attenuation and even stopping. The oscillation and stop changes of the oscillator are processed by the subsequent amplification circuit and converted into switch signals, triggering the driving components to achieve non-contact detection purposes
- ZHUOXIN
- 24v-110v-220v-380v
- IP65
- TT, Paypal, Credit card, Western union
- +86-15163766288
- The proximity sensor XS2 30BLNAL2C C24V consists of three main parts: oscillator, switch circuit, and amplifier output circuit. The oscillator generates an alternating magnetic field. When the metal target approaches this magnetic field and reaches the sensing distance, eddy currents are generated within the metal target, leading to oscillation attenuation and even stopping. The oscillation and stop changes of the oscillator are processed by the subsequent amplification circuit and converted into switch signals, triggering the driving components to achieve non-contact detection purposes
Description
Proximity sensor XS2 30BLNAL2C C24VXS106B3PAL2TQ XS106B3PAL2TQ XS106B3PAL2TQ XS106B3PAL2TQ
XS106B3PAM8TQ XS106B3PAM8TQ XS106B3PAM8TQ XS106B3PAM8TQ XS106B3PAM8TQ XS106B3PAM8TQ
XS106BLNAL2 XS106BLNAL2 XS106BLNAL2 XS106BLNAL2
XS106BLNAL5 XS106BLNAL5 XS106BLNAL5 XS106BLNAL5 XS106BLNAL5 L5
XS106BLNBL2 XS106BLNBL2 XS106BLNBL2 XS106BLNBL2 XS106BLNBL2
XS106BLNBL5 XS106BLNBL5 XS106BLNBL5 XS106BLNBL5 XS106BLNBL5
XS106BLPAL2 XS106BLPAL2 XS106BLPAL2 XS106BLPAL2
XS106BLPAL5 XS106BLPAL5 XS106BLPAL5 XS106BLPAL5 XS106BLPAL5
XS106BLPBL2 XS106BLPAL5 PBL2 XS106BLPBL2 XS106BLPBL2 XS106BLPBL2
XS106BLPBL5 XS106BLPBL5 XS106BLPBL5 XS106BLPBL5 XS106BLPBL5
XS108B3NAL2TQ XS108B3NAL2TQ XS108B3NAL2TQ XS108B3NAL2TQ XS108B3NAL2TQ XS108B3NAL2TQ< XS108B3NAM8TQ XS108B3NAM8TQ XS108B3NAM8TQ XS108B3NAM8TQ XS108B3NAM8TQ XS108B3NAM8TQ XS108B3PAL2TQ XS108B3PAL2TQ XS108B3PAL2TQ XS108B3PAL2TQ XS108B3PAL2TQ XS108B3PAL2TQ XS108B3PAM12TQ XS108B3PAM12TQ XS108B3PAM12TQ XS108B3PAM12TQ XS108B3PAM12TQ XS108B3PAM12TQ XS108B3PAM12TQ XS108B3PAM8TQ XS108B3PAM8TQ PAM8TQ XS108B3PAM8TQ XS108B3PAM8TQ
XS108BLNAL2 XS108BLNAL2 XS108BLNAL2 XS108BLNAL2
XS108BLNAL2C XS108BLNAL2C XS108BLNAL2C XS108BLNAL2C
XS108BLNAL5 XS108BLNAL5 XS108BLNAL5 XS108BLNAL5 XS108BLNAL5 XS108BLNAL5 XS108BLNAL5 XS108BLNAL5
XS108BLNAL5C XS108BLNAL5C XS108BLNAL5C XS108BLNAL5C BLNAL5C XS108BLNAL5C
XS108BLNAM12 XS108BLNAM12 XS108BLNAM12 XS108BLNAM12 XS108BLNAM12 Introduction Inductive proximity switch consists of three main parts: oscillator, switching circuit, and amplification output circuit. The oscillator generates an alternating magnetic field. When the metal target approaches this magnetic field and reaches the sensing distance, eddy currents are generated within the metal target, leading to oscillation attenuation and even stopping. The oscillation and stop changes of the oscillator are processed and converted into switch signals by the subsequent amplification circuit, triggering the driving device to achieve non-contact detection purposes. Principle 2 of this paragraph: Introduction to the working principle of Hall proximity switch: When a metal or semiconductor thin film with current is vertically placed in a magnetic field, there will be a potential difference between the two ends of the film, which is called the Hall effect. The difference in potential between the two ends is called the Hall potential U, which is expressed as U=K& Miot; I&miot; B/where K is the Hall coefficient, I is the current passing through the thin film, B is the magnetic induction intensity of the external magnetic field (Lorentz force), and is the thickness of the thin film. It can be seen that the sensitivity of the Hall effect is directly proportional to the magnetic induction intensity of the applied magnetic field. Hall switch belongs to this type of active magneto electric converter device. It is made using integrated packaging and assembly technology based on the Hall effect principle. It can easily convert magnetic input signals into practical application signals, while also meeting the requirements of easy operation and reliability in industrial applications. The input of the Hall switch is characterized by the magnetic induction intensity B. When the value of B reaches a certain level (such as B1), the trigger inside the Hall switch flips, and the output level state of the Hall switch also flips. The output terminal generally uses transistor output, similar to sensors, including NPN, PNP, normally open, normally closed, latch type (bipolar), and dual signal output. Hall switches have characteristics such as contactless, power consumption, long service life, and response frequency. They are internally sealed with epoxy resin, so they can work reliably in various harsh environments. Hall switches can be applied to proximity sensors, pressure sensors, odometers, etc., as a new type of electrical accessory. The working principle of linear proximity sensor: Linear proximity sensor is a linear device belonging to metal induction. After power is turned on, an alternating magnetic field is generated on the sensing surface of the sensor. When a metal object approaches this sensing surface, eddy currents are generated in the metal, which absorbs the energy of the oscillator, causing the output amplitude of the oscillator to decay linearly. Then, based on the change in attenuation, the purpose of non-contact object detection is achieved. The proximity sensor has sliding contacts and is not affected by non-metallic factors such as dust during operation. It also has power consumption and long lifespan, and can be used in various harsh conditions. Linear sensors are mainly used for intelligent control of analog quantities in automated equipment lines. Inductive proximity switch proximity sensor XS2 30BLNAL2C C24V working principle Inductive proximity switch consists of three main parts: oscillator, switch circuit, and amplifier output circuit. The oscillator generates an alternating magnetic field. When the metal target approaches this magnetic field and reaches the sensing distance, eddy currents are generated within the metal target, leading to oscillation attenuation and even stopping. The oscillation and stop changes of the oscillator are processed by the subsequent amplification circuit and converted into switch signals, triggering the driving device to achieve non-contact detection.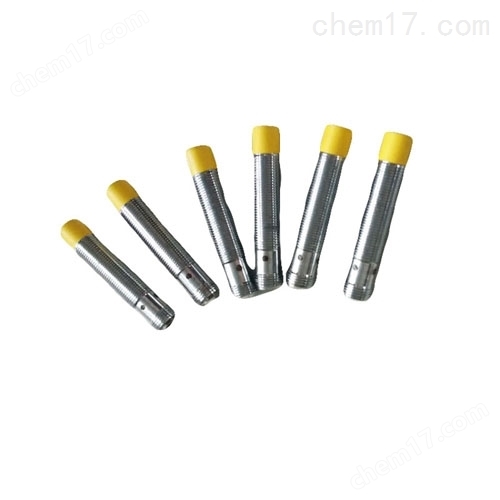
XS106B3PAM8TQ XS106B3PAM8TQ XS106B3PAM8TQ XS106B3PAM8TQ XS106B3PAM8TQ XS106B3PAM8TQ
XS106BLNAL2 XS106BLNAL2 XS106BLNAL2 XS106BLNAL2
XS106BLNAL5 XS106BLNAL5 XS106BLNAL5 XS106BLNAL5 XS106BLNAL5 L5
XS106BLNBL2 XS106BLNBL2 XS106BLNBL2 XS106BLNBL2 XS106BLNBL2
XS106BLNBL5 XS106BLNBL5 XS106BLNBL5 XS106BLNBL5 XS106BLNBL5
XS106BLPAL2 XS106BLPAL2 XS106BLPAL2 XS106BLPAL2
XS106BLPAL5 XS106BLPAL5 XS106BLPAL5 XS106BLPAL5 XS106BLPAL5
XS106BLPBL2 XS106BLPAL5 PBL2 XS106BLPBL2 XS106BLPBL2 XS106BLPBL2
XS106BLPBL5 XS106BLPBL5 XS106BLPBL5 XS106BLPBL5 XS106BLPBL5
XS108B3NAL2TQ XS108B3NAL2TQ XS108B3NAL2TQ XS108B3NAL2TQ XS108B3NAL2TQ XS108B3NAL2TQ< XS108B3NAM8TQ XS108B3NAM8TQ XS108B3NAM8TQ XS108B3NAM8TQ XS108B3NAM8TQ XS108B3NAM8TQ XS108B3PAL2TQ XS108B3PAL2TQ XS108B3PAL2TQ XS108B3PAL2TQ XS108B3PAL2TQ XS108B3PAL2TQ XS108B3PAM12TQ XS108B3PAM12TQ XS108B3PAM12TQ XS108B3PAM12TQ XS108B3PAM12TQ XS108B3PAM12TQ XS108B3PAM12TQ XS108B3PAM8TQ XS108B3PAM8TQ PAM8TQ XS108B3PAM8TQ XS108B3PAM8TQ
XS108BLNAL2 XS108BLNAL2 XS108BLNAL2 XS108BLNAL2
XS108BLNAL2C XS108BLNAL2C XS108BLNAL2C XS108BLNAL2C
XS108BLNAL5 XS108BLNAL5 XS108BLNAL5 XS108BLNAL5 XS108BLNAL5 XS108BLNAL5 XS108BLNAL5 XS108BLNAL5
XS108BLNAL5C XS108BLNAL5C XS108BLNAL5C XS108BLNAL5C BLNAL5C XS108BLNAL5C
XS108BLNAM12 XS108BLNAM12 XS108BLNAM12 XS108BLNAM12 XS108BLNAM12 Introduction Inductive proximity switch consists of three main parts: oscillator, switching circuit, and amplification output circuit. The oscillator generates an alternating magnetic field. When the metal target approaches this magnetic field and reaches the sensing distance, eddy currents are generated within the metal target, leading to oscillation attenuation and even stopping. The oscillation and stop changes of the oscillator are processed and converted into switch signals by the subsequent amplification circuit, triggering the driving device to achieve non-contact detection purposes. Principle 2 of this paragraph: Introduction to the working principle of Hall proximity switch: When a metal or semiconductor thin film with current is vertically placed in a magnetic field, there will be a potential difference between the two ends of the film, which is called the Hall effect. The difference in potential between the two ends is called the Hall potential U, which is expressed as U=K& Miot; I&miot; B/where K is the Hall coefficient, I is the current passing through the thin film, B is the magnetic induction intensity of the external magnetic field (Lorentz force), and is the thickness of the thin film. It can be seen that the sensitivity of the Hall effect is directly proportional to the magnetic induction intensity of the applied magnetic field. Hall switch belongs to this type of active magneto electric converter device. It is made using integrated packaging and assembly technology based on the Hall effect principle. It can easily convert magnetic input signals into practical application signals, while also meeting the requirements of easy operation and reliability in industrial applications. The input of the Hall switch is characterized by the magnetic induction intensity B. When the value of B reaches a certain level (such as B1), the trigger inside the Hall switch flips, and the output level state of the Hall switch also flips. The output terminal generally uses transistor output, similar to sensors, including NPN, PNP, normally open, normally closed, latch type (bipolar), and dual signal output. Hall switches have characteristics such as contactless, power consumption, long service life, and response frequency. They are internally sealed with epoxy resin, so they can work reliably in various harsh environments. Hall switches can be applied to proximity sensors, pressure sensors, odometers, etc., as a new type of electrical accessory. The working principle of linear proximity sensor: Linear proximity sensor is a linear device belonging to metal induction. After power is turned on, an alternating magnetic field is generated on the sensing surface of the sensor. When a metal object approaches this sensing surface, eddy currents are generated in the metal, which absorbs the energy of the oscillator, causing the output amplitude of the oscillator to decay linearly. Then, based on the change in attenuation, the purpose of non-contact object detection is achieved. The proximity sensor has sliding contacts and is not affected by non-metallic factors such as dust during operation. It also has power consumption and long lifespan, and can be used in various harsh conditions. Linear sensors are mainly used for intelligent control of analog quantities in automated equipment lines. Inductive proximity switch proximity sensor XS2 30BLNAL2C C24V working principle Inductive proximity switch consists of three main parts: oscillator, switch circuit, and amplifier output circuit. The oscillator generates an alternating magnetic field. When the metal target approaches this magnetic field and reaches the sensing distance, eddy currents are generated within the metal target, leading to oscillation attenuation and even stopping. The oscillation and stop changes of the oscillator are processed by the subsequent amplification circuit and converted into switch signals, triggering the driving device to achieve non-contact detection.
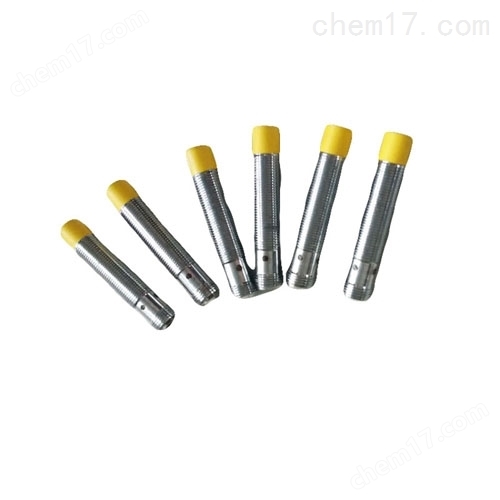
Tags
Get the latest price? We'll respond as soon as possible(within 12 hours)