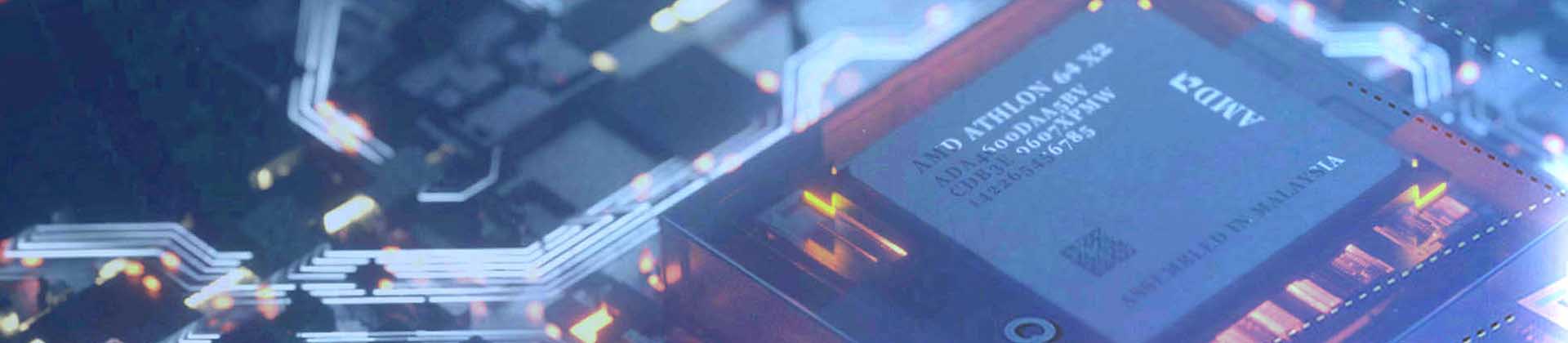
HJA-L position passive feedback displacement sensor
The principle of HJA-L passive position feedback displacement sensor is to use the collision of mechanical moving parts to make their contacts move, in order to connect or disconnect the control circuit and achieve certain control objectives. Usually, these types of switches are used to determine the position or position of mechanical movement, causing the moving machinery to automatically stop, move in reverse, change speed, or move back and forth according to a certain position or position.
- ZHUOXIN
- 24v-110v-220v-380v
- IP65
- TT, Paypal, Credit card, Western union
- +86-15163766288
- The principle of HJA-L passive position feedback displacement sensor is to use the collision of mechanical moving parts to make their contacts move, in order to connect or disconnect the control circuit and achieve certain control objectives. Usually, these types of switches are used to determine the position or position of mechanical movement, causing the moving machinery to automatically stop, move in reverse, change speed, or move back and forth according to a certain position or position.
Description
The principle of HJA-L position passive feedback displacement sensor is to use the collision of mechanical moving parts to make their contacts move to connect or disconnect the control circuit, achieving a certain control purpose. Usually, these types of switches are used to determine the position or position of mechanical movement, causing the moving machinery to automatically stop, move in reverse, change speed, or move back and forth according to a certain position or position. Construction: Composed of an operating head, contact system, and housing. Classification: It is divided into direct action (button type), rolling type (rotary type), micro action type, and combination type. Direct action HJA-L position switch: The operating principle is similar to that of a button, except that one is manual and the other is collided by moving parts. When the collision block on the external moving component presses the button, its contact will move. After the moving component leaves, under the action of the spring, its contact will automatically reset. Rolling position switch: When the blocking iron (collision block) of the moving machinery presses against the roller of the position switch, the transmission lever and the shaft rotate together, causing the cam to push the collision block. When the collision block hits a certain position, it pushes the micro switch to move at a fast speed. When the stopper on the roller is removed, the reset spring resets the position switch. This is a single wheel automatic return position switch. The dual wheel rotary position switch cannot automatically restore itself. It relies on the collision of the blocking iron with another roller when the moving machinery moves in the opposite direction to restore it. Proximity switch: also known as contactless position switch, it not only has a contact position switch to complete position control and limit protection, but can also be used for counting, speed measurement, liquid level control, part size detection, automatic connection of processing programs, etc. Due to its non-contact triggering, action speed, ability to operate at different detection distances, stable and non pulsating signals, stable and reliable operation, long service life, repeated positioning, and ability to adapt to harsh working environments, it is widely used in industries such as machine tools, textiles, printing, and plastics. Proximity switches are classified according to their working principles, including frequency oscillation type, Hall type, capacitance type, differential coil type, permanent magnet type, etc. Among them, frequency oscillation type is commonly used. Permanent magnet type: It uses the suction force of a magnet to drive the tongue spring switch and output a signal. Differential coil type: It utilizes the changes in eddy currents and magnetic fields generated when the object being tested approaches, and operates by comparing the difference between the detection coil and the comparison coil. Capacitive proximity switch: mainly composed of capacitive oscillator and electronic circuit, its capacitance is located at the sensing interface. When an object approaches, it will oscillate due to changing its coupling capacitance value, resulting in oscillation or stopping oscillation, causing the output signal to change. Capacitive proximity switches can be triggered by various materials, such as solid, liquid, or powdered objects. Hall proximity switch: It operates by converting magnetic signals into signal outputs, and its output has a memory retention function. The internal magnetic components only respond to the magnetic field perpendicular to the sensor end face. When the magnetic pole S is facing the proximity switch, the output of the proximity switch produces a positive jump, and the output is a level. If the magnetic pole N is facing the proximity switch, the output is a level. Proximity switch: mainly composed of piezoelectric ceramic sensors, electronic devices for transmitting and receiving reflected waves, and programmable bridge switches for adjusting the detection range. Suitable for detecting unreachable or unreachable targets, its control function is not affected by factors such as sound, electricity, and light. The detection target can be a solid, liquid, or powder object, as long as it can reflect. Frequency oscillation proximity switch: It is triggered by metal and mainly consists of a frequency oscillator, integrated circuit or transistor amplifier, and output. Its working principle is that the coil of the oscillator generates an alternating magnetic field on the surface of the switch. When a metal object approaches this surface, the eddy currents generated inside the metal object will absorb the energy of the oscillator, causing it to stop oscillating. The oscillation and stop signals of the oscillator are amplified and converted into binary switch signals, and output switch control signals. Selection and installation of limit switches: (1) Choose the type according to the application situation and control object. (2) Choose the appropriate operating head form based on the force and displacement relationship between the mechanical and limit switches. (3) Select the series based on the rated voltage and rated current of the control circuit. (4) Choose the protective form according to the installation environment. The installation of limit switches (1) The limit switches should be securely fastened to the mounting plate and mechanical equipment without any shaking. (2) The position of the limit switch should be accurate during installation, otherwise position control cannot be achieved. Shandong Zhuoxin Machinery Co., Ltd. is a company mainly engaged in industrial control electrical appliances, including proximity switches, photoelectric switches, Hall IC Hall switches, Hall components, two-stage deviation switches, bidirectional rope switches, speed detectors, belt slip switches, anti rotation material levels, belt longitudinal tear switches, mining magnetic wellbore switches, tilt switches, chute blockages, sound and light warning devices, limit switches, travel switches, elevator switches, elevator weighing sensors, solenoid valve coils, gear sensors, temperature resistant passive feedback sensors, cold and hot metal sensors, speed rotation monitoring sensors, speed sensors, proximity sensors, photoelectric sensors, contactless magnetic switches, magnetic proximity switches, belt conveyor control cabinets, etc. We collect, trial produce, and develop industrial control electrical appliances. Manufacturing, sales and integration. 

Tags
Get the latest price? We'll respond as soon as possible(within 12 hours)